Laser OES vs. Spark OES: A Direct Comparison
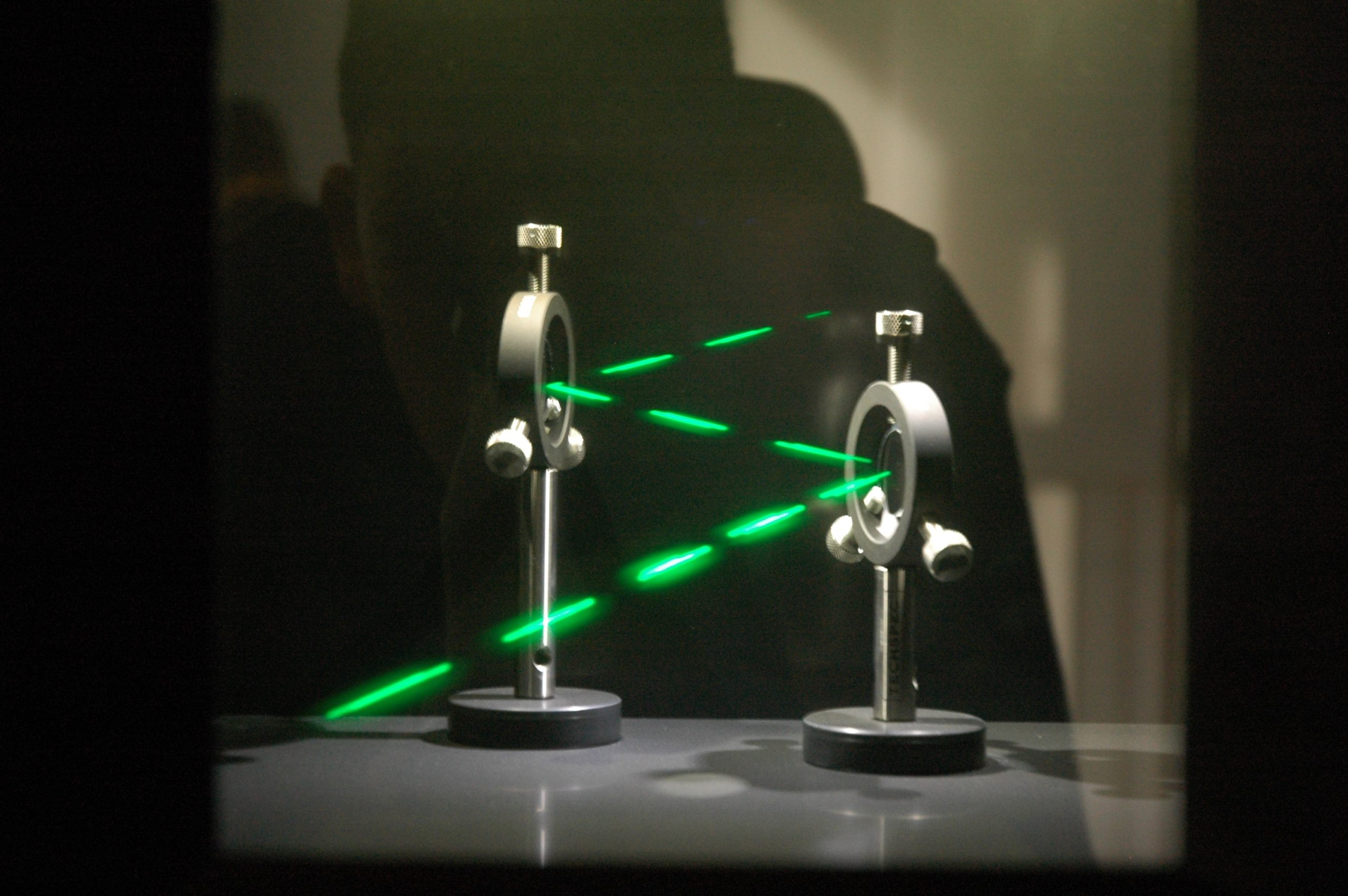
[powerpress]
It’s easy for manufacturing professionals (including myself) to gravitate to the old adage, “If it ain’t broke, don’t fix it.” However, when it comes to spark OES versus laser OES technology, I lean towards the latter.
Spark OES systems have been around for decades now, and the manufacturing industry hasn’t seemed too keen on changing that.
But what if there was something quicker and easier to use?
The big question I’ve set out to answer is:
What’s the difference between spark OES and laser OES for PMI? The difference between spark OES and laser OES is the excitation source. Spark OES uses bursts of high current sparks to turn the metal into plasma and read the light signature. Laser OES uses high-energy laser pulses to create the plasma needed for positive material identification.
I hope by going through this post — and, maybe listening to the podcast it’s based on — you’ll gain a better understanding of spark OES versus laser OES.
In this blog, we’ll cover:
- The basics of positive material identification (PMI) and optical emission spectroscopy (OES)
- The origins of spark OES and laser OES technology
- A side-by-side comparison of spark OES and laser OES
- The advanced digital platform used with laser OES
Let’s get started!
This post is based on a podcast featuring Chris Carolan of the Metal Analysis Group. To hear this episode and more like it, subscribe to The Manufacturing Show on Apple Podcasts, Spotify, or wherever you listen to podcasts.
Why is positive material identification important?
Positive material identification (PMI) is important for a variety of reasons. Mostly, PMI is essential because it verifies the world around us. Think about all the structures made out of metal!
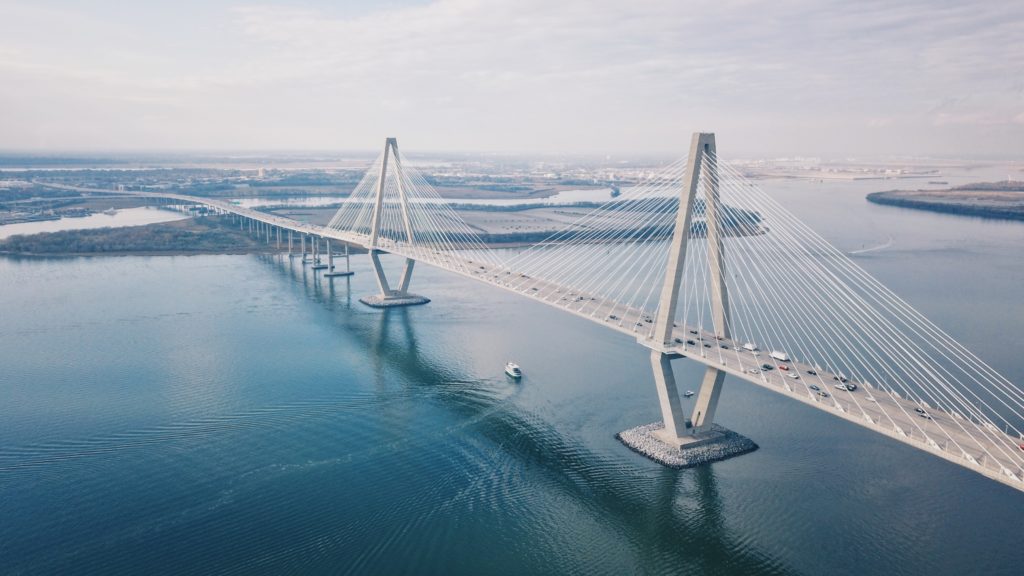
As we discussed in an earlier post, PMI is defined as follows:
Positive material identification (PMI) testing is the analysis of a material, normally a metallic alloy, to confirm the material is consistent with what the end-user specified.
Mobile OES is one of the most commonly used techniques for PMI testing.
Avoidable disasters
In 2005, a deadly explosion erupted at BP’s Texas City refinery, killing 15 people and injuring another 180.
The reason? Through many organizational and technical mistakes, a hydrocarbon vapor cloud eventually formed and caught fire, resulting in a massive explosion.
Did BP learn its lesson? Not quite. Just a few months later, a hydrogen gas heat exchanger pipe overheated and burst on the exact same refinery. An enormous fireball was the product.
After an investigation, the Chemical Safety Board found that a contractor had swapped a low-alloy steel part with a carbon steel pipe elbow. Fortunately, only one person received minor injuries from the fireball.
100% PMI testing
You can probably see how PMI testing for 100 percent of materials is the industry standard now.
This means every single piece of the lot or batch needs to be tested before handing over to the customer requiring 100 percent PMI.
Other disasters positive material identification prevents:
- Oil spills
- Airplane crashes
- Bridges collapsing
- Aerospace accidents
- Construction mishaps
- Vehicle accidents
- Processing plant crises
- Medical device errors
Seriously, anything consisting of metal needs to be positively identified. That’s why the optical emission spectrometer has been a popular choice for comprehensive metal testing in the field.
Optical emission spectroscopy (OES) for PMI
Because of its accuracy and relatively non-destructive qualities, OES is a preferred method for PMI testing.
OES parts
Any kind of OES analyzer consists of three main parts:
- the electrical or laser source
- an optical detector
- a computer system
Whether it uses an electrical source or a laser, the OES has to be able to heat a metal sample to extremely high temperatures in order to excite the atoms.
How it works
Simply put, the steps an optical emission spectrometer uses are as follows.
- Charging up the atoms — The OES uses an electrical or laser-based source to excite the atoms within the material sample. The light the sample then emits reveals its elemental composition.
- Measuring the intensity — The intensity of each light wavelength emitted is then measured and graded by a corresponding detector. Each wavelength’s intensity tells you how much of one element is present in the material.
- Analyzing the overall composition — A software system intakes the wavelength information and generates the concentration levels of the elements.
The evolution of the OES
To understand both types of OES, it’s important to understand how the process has evolved.
- Flame testing — In the early 1900s, manufacturers used a flame as the heating source in OES. The light produced from the charged atoms would help to identify the material’s elemental composition.
- Spark OES — By the 1960s, metal production labs were using a spark to positively identify materials. Spark OES was much more controllable and accurate than flame OES. Spark OES is still the most widely used method for comprehensive PMI testing.
- Laser OES — While it’s not yet widely adopted, laser OES is a more efficient way of positively identifying materials. Modern advancements in laser technology have allowed for lasers to replace sparks as the excitation source in OES testing equipment.
Laser OES is the newest PMI technique and, therefore, hasn’t made much ground yet.
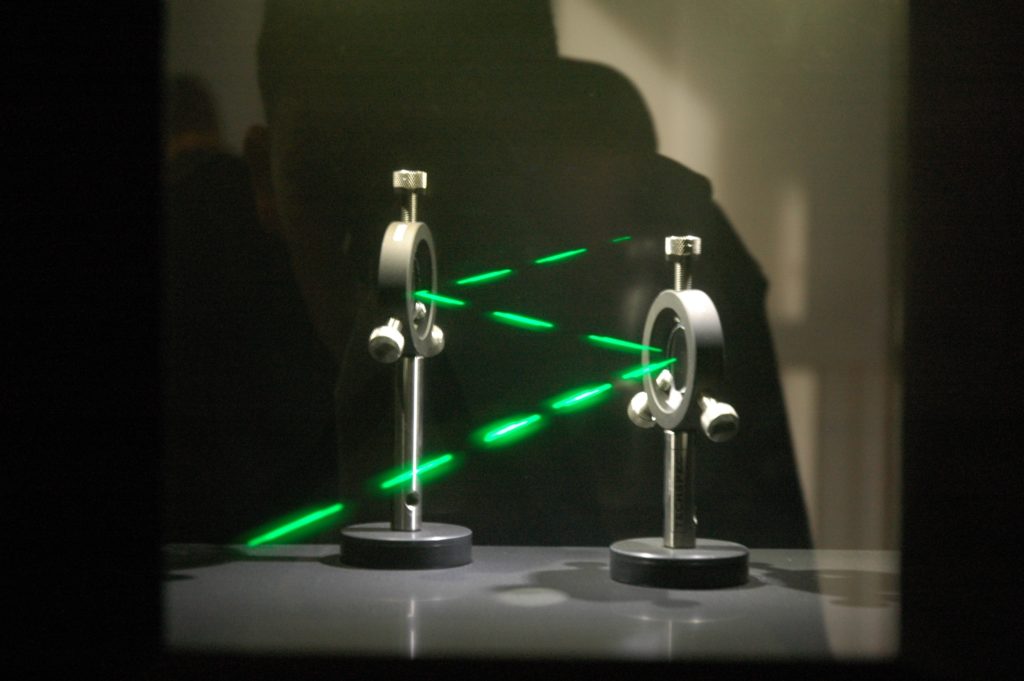
The thing is, this new process for testing metal alloys is so revolutionary that I want everyone to know about it! I also understand it can be difficult to part with the old, trusty way of doing things.
So, I thought it might help to look at spark OES and laser OES side-by-side.
What is a spark OES?
A spark optical emission spectrometer is used to identify the composition of a material by way of a spark.
The spark OES process
Essentially, bursts of high current sparks are discharged to excite the atoms within the sample material. The optical system, then, separates the different wavelengths of light before they reach the detector.
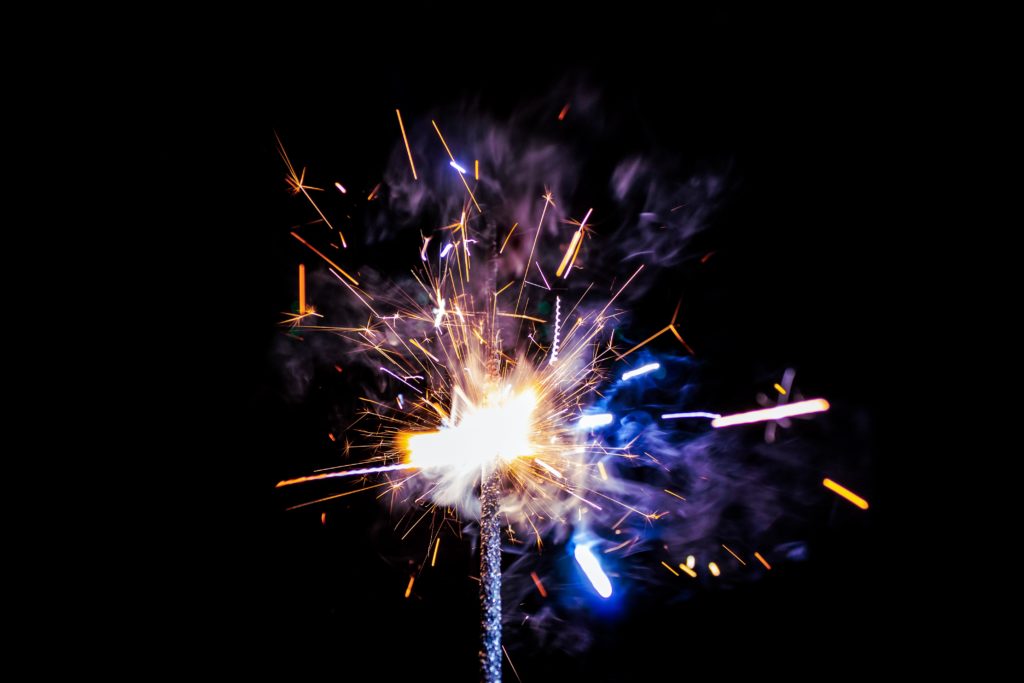
Next, the detector system measures the intensities of the lights being emitted. The computer system takes those measurements, stores them, and produces the elemental results.
"OES is generally the accepted practice when you need low levels of carbon, sulfur, phosphorus, and nitrogen in a variety of different metals."
Chris Carolan
This process has become more and more accurate as technology has advanced.
Spark OES brands
Brands that manufacture the spark OES system include:
- Hitachi (formerly Oxford)
- SPECTRO
- Thermo ARL
- Bruker
Since its beginning in the mid 20th century, spark OES has been the golden standard for identifying materials.
But now, there’s a new kid on the block, and his name is laser OES.
What is a laser OES?
Laser optical emission spectroscopy is a laser-based PMI technique that provides a full chemical composition of metal alloys.
The laser OES process
The laser OES technique uses high-energy laser pulses to excite the atoms within a sample. The plasma light that’s emitted shows “spectral signatures” of the sample’s elements.
Not unlike spark OES, laser OES transfers light intensity data to a computer system. This makes it easier for humans to interpret the elemental composition of the material.
Laser OES brands
Currently, the German-based QuantoLux is the only manufacturer of laser OES technology. QuantoLux creates benchtop and portable versions of the laser OES.
Laser OES vs. spark OES
So far, these two technologies don’t seem that different. While the fundamental ideas behind each are similar, there are some stark contrasts.
Let’s take a closer look at the pros and cons of using spark OES technology versus a laser OES system.
Spark OES pros
- It’s a proven technique for positively identifying materials including carbon, boron, phosphorus, sulfur, and nitrogen.
- Only a portion of the material is destroyed in testing.
- There are several manufacturers that produce spark OES systems.
Spark OES cons
- It tends to take a long time to test materials.
- It can be difficult to keep the probe in place during long test times.
- Even the mobile OES system is still bulky and difficult to move from place to place. (35+ lbs plus the argon gas tank. Oof.)
- It’s a potential safety hazard to move the spark OES system.
- Restocking the high purity argon gas can be cumbersome and needs to be done quite often.
- The instrument’s stability is easily compromised by the environment.
- It needs time to reacclimate when moved to a different location, especially with differences in temperature.
- Preparing samples for the spark OES to test is rather laborious.
- The electrode requires maintenance very regularly.
- There are no small samples tested because of the size of the burn site.
- A long recalibration and standardization process is needed.
"Traditional spark OES is very temperamental when it comes to environmental changes."
Chris Carolan
Laser OES pros
- The laser OES system can take 10 measurements per minute or 300-600 measurements per hour.
- The instrument is small, handy, and easy to transport. (Less than 15 lbs including the argon tank. Light as a feather!)
- There is no safety hazard when it comes to moving a laser OES system.
- It only takes a very light bottle of argon gas that lasts for over 1,000 measurements.
- The bottle for argon is small and easily refillable.
- Its internal battery is lightweight and rechargeable.
- The instrument does not require any time to reacclimate itself when moved from place to place.
- The laser OES does not use high voltages or extremely high temperatures to test materials.
- Metal samples take less preparation in order to be tested.
- There’s no electrode to spend money or time maintaining, cleaning, sharpening, or replacing.
- The laser OES microspot can test small parts such as nuts and bolts.
- It can recalibrate using a single sample in seconds.
- The data management and software are lightyears ahead of the traditional spark OES system. (More on that in a second.)
Laser OES cons
- Only one brand currently manufactures laser OES technology.
- There’s already a waiting list for laser OES systems.
- It’s a brand new technology needing more real-world feedback.
As laser OES technology continues to be adopted around the world, user feedback will be used to keep it at the top of its game.
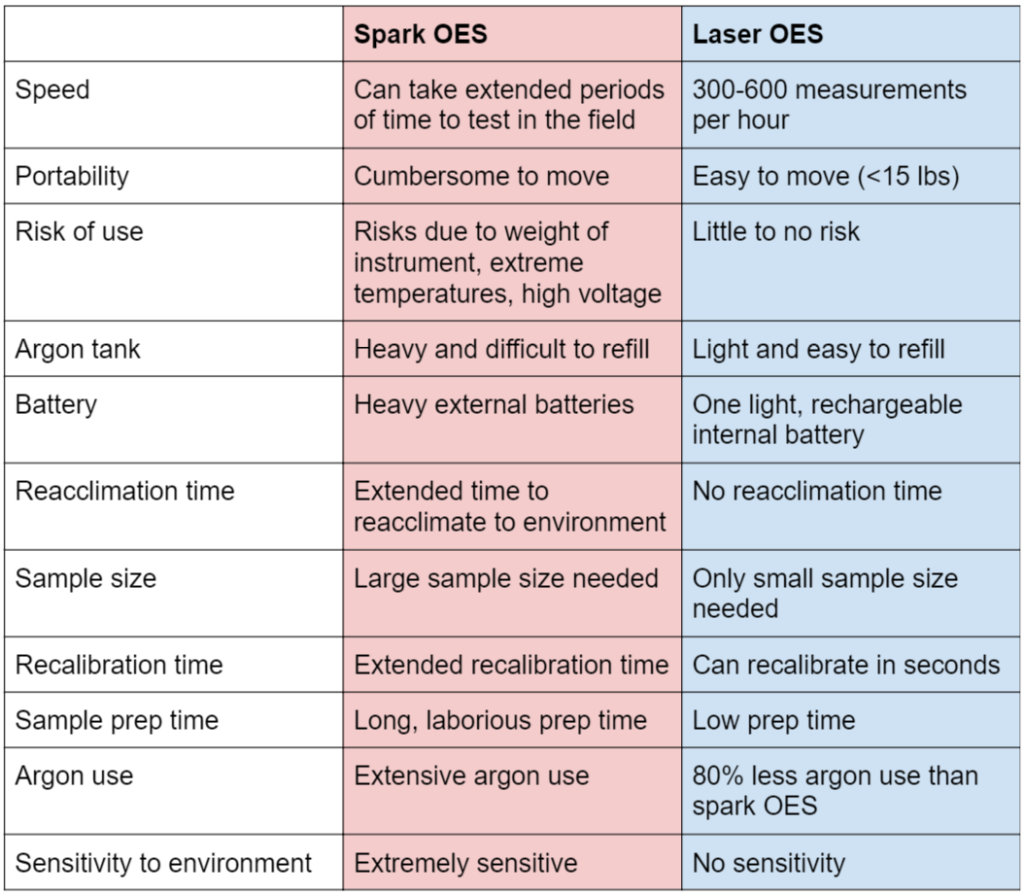
Now, you might think this is a pretty lopsided match-up. You’d be right!
Laser OES is the real deal and it’s coming for your spark OES system.
We could call the contest there. But, in the digital age, PMI testing equipment is only as good as the user experience and its digital platform. So, let’s check it out.
Data management and software
The improvement of data management and software with laser OES technology is so great that it deserves its own segment.
Be prepared to be impressed!
The digital platform
Laser OES uses an advanced digital platform to control, maintain, and observe the technology and its results.
Major highlights of the digital platform include…
… the ability to add new programs and calibrations remotely. That’s right: No more sending the instrument back and forth or shipping around service technicians.
… proactive component monitoring. Unexpected downtime? Not with this technology. Identify a potential issue before it ever becomes a problem.
… virtual support. Get remote assistance for your spectrometer any time, anywhere.
Doesn’t that sound one million times better than the spark OES system? Surprisingly, there are still more awesome things to mention.
Software and data
The software that the laser OES technology uses was designed like your mobile device’s (i.e. iOS, Android). So, what exactly does that mean?
An unmatched user experience (among other benefits).
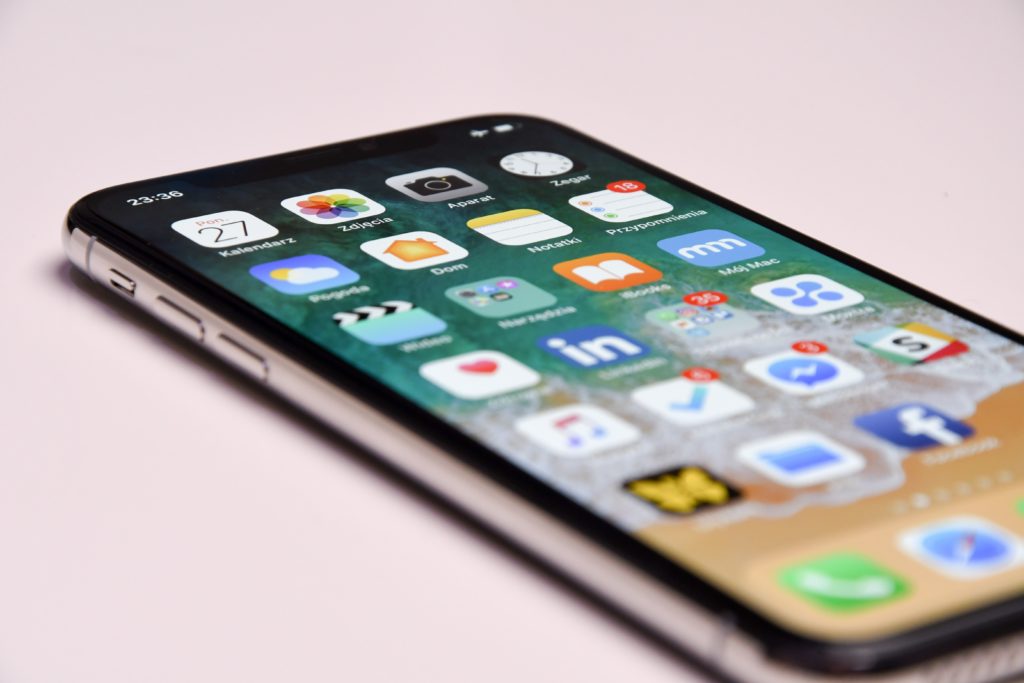
- The software is always updated with easy download and installation.
- It’s as easy to use as your mobile device.
- You can choose to store your data in the security of the cloud or on-premise.
- You can easily share data your system has collected with anyone, anywhere, even in real-time.
- It’s simple to integrate M2M (machine-to-machine) communication so your whole facility is on the same page.
- Connect and collaborate with the online community of laser OES users to discover new tricks, insights, and even customized calibrations.
Sounds pretty great, right?
Now you know why I was so pumped for laser OES technology at the start of this post!
Welcome to the future of manufacturing
You may be still weighing the differences between the spark OES system and laser OES technology. Fair enough; it’s a big decision.
Even so, to stay on the leading edge of the manufacturing industry, I’d strongly advise you to consider laser OES.
Not only is it more convenient, reliable, and less wasteful — it’s faster, more resilient, and smarter too.
The ball is in your court now. Will you master your metal?
For more information on laser OES and spark OES systems, subscribe to The Manufacturing Show on Apple Podcasts, Spotify, or wherever you listen to podcasts.
By Chris Carolan, Consultant at Metal Analysis Group
Chris serves as the Inside Sales and Marketing Consultant for MAG. He has worked in Elemental Analysis for Oil & Gas and related industries for over 12 years connecting with customers at each point in the supply chain. Spending most of his career in reference material manufacturing, Chris has learned a great deal about troubleshooting specific customer scenarios and applications.
Gaining experience in production, quality control, marketing, and sales, Chris is eager to put that experience and knowledge to use by helping customers create unique solutions that save money, reduce risk, and increase profits.