Preventative Maintenance for PMI Testing Equipment is a MUST
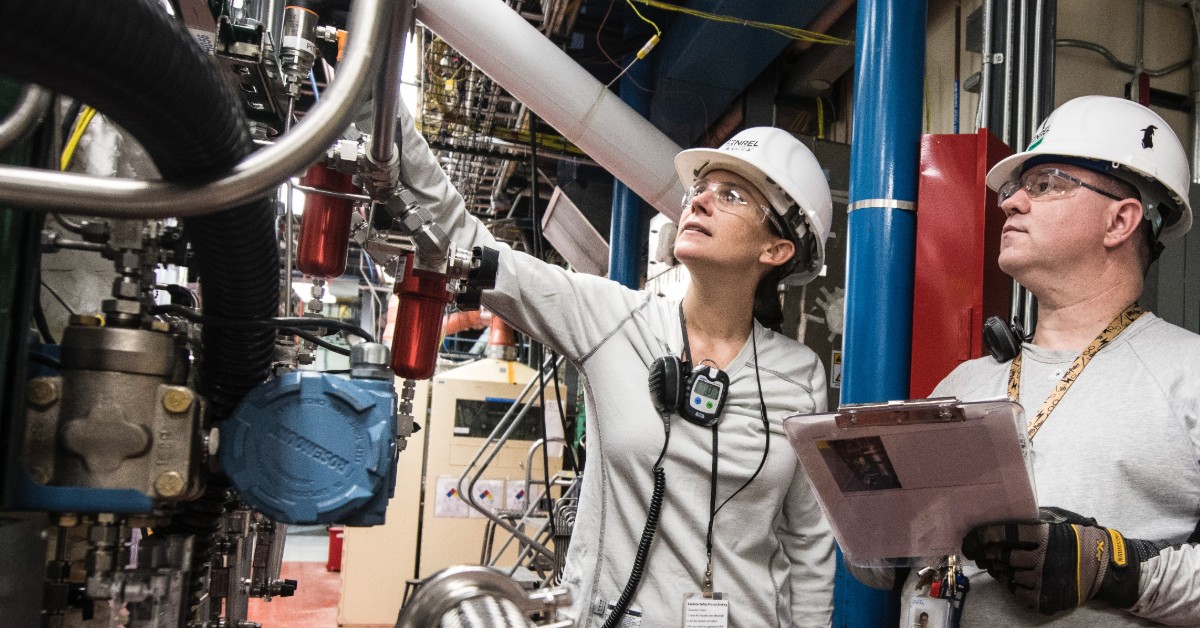
You take your car to the shop to get its oil changed. You go to the dentist to get your teeth cleaned (hopefully). You take your pup to the vet for booster shots.
These are all preventative measures. The same type of preventative maintenance should be done for your PMI testing equipment.
Sure, sometimes preventative maintenance can feel like a hassle. But it’s nothing compared to what would happen if you didn’t do it.
The big question we’re answering today is…
Why does preventative maintenance for PMI testing equipment matter? Preventative maintenance for PMI testing equipment is a must because a compromised analyzer can lead to expensive material mix-ups, downtime, and, potentially, catastrophes.
To take a closer look at preventative maintenance for PMI testing equipment, we’re going to cover:
- Real-world examples that demonstrate how crucial it is to maintain PMI equipment
- How to avoid costly errors with annual instrument recertification
- The differences between instrument recalibration and recertification
- Tips to maintain PMI testing equipment
Let’s get to it!
Psst: This post is based on a podcast with co-host Chris Carolan. To hear this episode (and more like it), subscribe to The Manufacturing Show on Apple Podcasts, Spotify, or wherever you listen to podcasts.
So, you purchased a metals analysis instrument
Your company decided to invest in an analyzer for positive material identification (PMI) — that’s fantastic! You’re ready to ensure the parts or products you’re supplying are meeting expectations.
You’ve completed the initial training for whichever PMI testing technique you chose. You trust that the instrument is going to give you accurate results right out of the box. It’s brand new, isn’t it?
Well, you’ve only really done half of the analysis. It’s imperative you confirm that the PMI instrument is giving you the correct results.
“No analytical instrument maintains its original calibration accuracy or precision indefinitely.”
Chris Carolan
To drive this point home, I’m sharing a few real-life examples that demonstrate the importance of testing and maintaining PMI equipment.
Example #1: The demo that went right
In this first example, I was measuring a variety of samples with a PMI instrument in a demonstration for a potential customer.
Inconsistent results
Some of the results I was getting were consistent with what the customer had gotten with their own analyzer and some were not. In each case, the instrument the customer was using was less precise than mine.
The problem
The customer and I were getting different results because I was using an instrument that had just been cleaned, recertified, and had its calibration verified with a check sample.
The customer’s unit was pulled out of a box and switched from off to on. Testing the check sample wasn’t a regular practice — it wasn’t even in the instrument box.
The customer had no idea of the condition of the instrument. Any number of issues could have caused the discrepancies.
Fortunately, I was able to help the customer realize the instrument they were using was not performing properly.
What went wrong
Here you have a blind acceptance of the results of the instrument. There was no prequalification of the instrument, no maintenance, and no idea of the instrument’s current condition.
Example #2: Different instruments, same results
In this instance, Company A had delivered finished materials to Company B.
Consistent results
When Company B measured the materials, they came to the same conclusions Company A had except with a different PMI instrument entirely.
Not only were the brands of tools different, but they were literally different PMI techniques.
How they did it
How did the companies get the same results?
By religiously maintaining the instruments and their calibrations. This attention to detail rewarded them with reliable results regardless of technology. Therefore, you have a positive result based on the tool owners’ commitment to properly maintaining the instruments.
Example #3: Same company, different results
In this last example, two facilities within the same company using identical PMI tools were testing the same material manufactured at the separate facilities. They produced different results.
Same company. Same PMI instruments. Same material. Separate environments. Different results.
What went wrong
The reason the two instruments did not match was a result of a very specific problem related to not properly scheduling annual instrument maintenance.
A small problem developed in one of the systems, which shifted the instrument’s calibration enough to cause erroneous results.
What we can learn from this
PMI instruments — no matter how large or small — are complex systems. Even a small issue can produce unreliable results.
To avoid scenarios like this one:
- Test check samples regularly, on a consistent schedule if possible
- Follow manufacturer recommended recalibrations and preventative maintenance schedules
- Schedule annual maintenance and recertification services
By following these suggestions, you ensure the data your instrument produces is accurate and reliable.
How to avoid costly errors with annual instrument recertification
Annual instrument recertification is absolutely necessary, but errors can be very costly. Luckily, there are ways to avoid those mistakes.
Analytical instrumentation
Here at Metal Analysis Group, we specialize in providing analytical instrumentation for the metals industry, whether it be primary metal production, product fabrication, or scrap.
The thing is, no analytical instrument can maintain its original calibration accuracy or precision forever.
Slowing the loss of accuracy
Whether the system is exposed to intensive use in extreme conditions or occasional use in a controlled environment, the factory calibration will eventually deviate from the original performance.
The question isn’t if it deviates. The only questions are when, how far, and at what cost to the company’s bottom line. That’s just the nature of machines.
In order to reduce the loss of instrument accuracy and precision, all instrument manufacturers provide…
- Maintenance manuals
- Check samples
- Sometimes recalibration standards
These resources are meant to prolong the instrument’s time between recalibration and recertification.
However, eventually, all instruments will reach the point where a professional recalibration and recertification is required.
Recalibration & recertification
All quality management systems recognize that periodic instrument recalibration and recertification is required.
So, quality management systems like those found in ISO-9001 usually require the NIST recommended yearly recalibration and recertification. If you’re using a PMI instrument in a high-production or unstable environment, a more aggressive approach may be necessary.
“Some service divisions are driven by profits and not necessarily the success of their customers.”
Chris Carolan
At this point, we need to make some distinctions: What are the differences between recalibration and recertification?
Recertification is the process by which an instrument of unknown accuracy and precision is tested against a Certified Reference Material of established value and precision.
Recalibration is the procedure that might follow to rectify a lack of agreement between the instrument’s results and the results expected from the Certified Reference Material.
All recalibration procedures require some maintenance to be completed prior to adjusting to the instrument’s calibration. This is done so that all wear and tear on the tool have been addressed before going forward with recalibration.
Accuracy & precision
There’s also a notable distinction between the terms accuracy and precision.
Accuracy refers to how close the instrument’s test result comes to the actual value of the Certified Reference Material.
Precision refers to how close the instrument comes to repeating the exact same test result when multiple tests of the Certified Reference Material are completed.
These are important principles to understand because they give significant information about the overall health of the analytical instrument.
Schedule PMI instruments for annual maintenance
You wouldn’t let your teeth fall out would you? And you probably wouldn’t let your dog get sick when a simple booster shot is all it takes to keep him well.
Why would you allow your PMI instrument to fail when you know it’s going to cost you dollars, downtime, and sometimes much worse?
The main takeaway I hope you gain from this article is to schedule preventative maintenance for your PMI testing equipment. You should be conducting at least an annual recertification and recalibration, if not more often for certain types of analyzers.
It’s crucial for your business, your team, and your customers.
Keep mastering your metals!
To learn more about PMI techniques, subscribe to The Manufacturing Show on Apple Podcasts, Spotify, or wherever you listen to podcasts.