What is Positive Material Identification (PMI)?
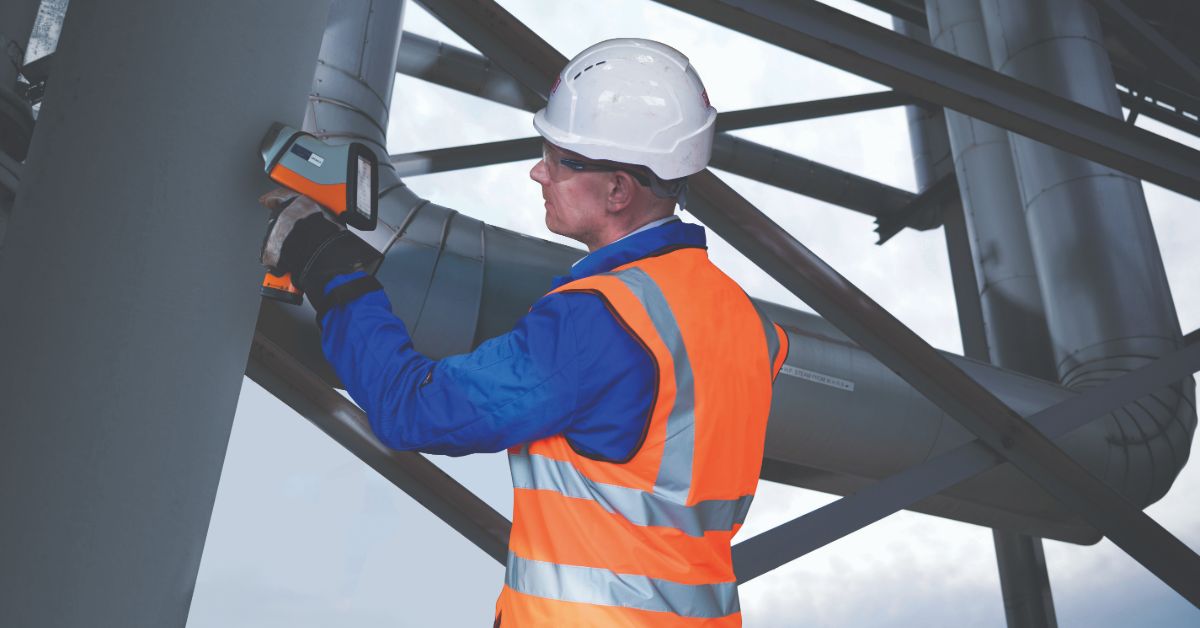
By Chris Carolan, Consultant at Metal Analysis Group
Positive material identification (PMI) helps us verify the world around us. That's why it’s tough for me to hear about accidents in the news caused by faulty parts and materials.Take, for example, the most recent SpaceX dilemma that caused Elon Musk’s rocket company to cut ties with PMI Industries. Because of falsified metal tests, faulty parts were shipped to SpaceX needed to build their Falcon 9 and other Falcon Heavy rockets.[caption id="attachment_13086" align="aligncenter" width="1200"]
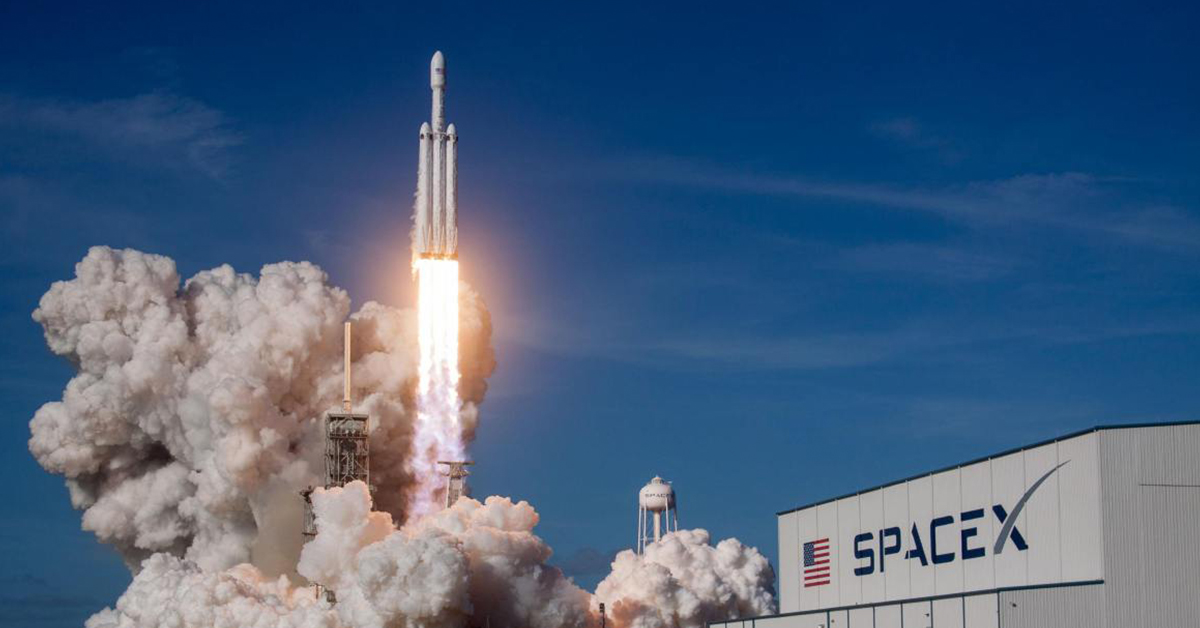
via Unsplash[/caption]It’s possible that as many as 10 of SpaceX’s government missions have been impacted by the defective materials, including those with NASA, the Air Force, and NOAA.That’s an avoidable mistake with a huge impact. PMI Industries is now out of business.With the right positive material identification (PMI) testing in place, fatal disasters can be prevented. That’s why I’ve dedicated this series of The Manufacturing Show to #MastersofPMI.In the first episode, I go over the basics of PMI testing, including answering questions like…What is positive material identification (PMI) testing? Positive material identification (PMI) testing is the analysis of a material, normally a metallic alloy, to confirm the material is consistent with what has been specified by the end-user.In this article, we’re going to cover:
- what positive material identification (PMI) testing is
- why PMI testing is important
- when you need PMI testing
- how to conduct a PMI test
- the cost of PMI testing
- the evolution of PMI testing
Let’s jump in!Psst: This post is based on a podcast with co-host Chris Carolan. To hear this episode (and more like it), subscribe to The Manufacturing Show on Apple Podcasts, Spotify, or wherever you listen to podcasts.
What is positive material identification (PMI) testing?
Positive material identification (PMI) testing is the examination of a material, usually a metallic alloy, to confirm the material is consistent with the user’s request.[caption id="attachment_13063" align="aligncenter" width="1200"]
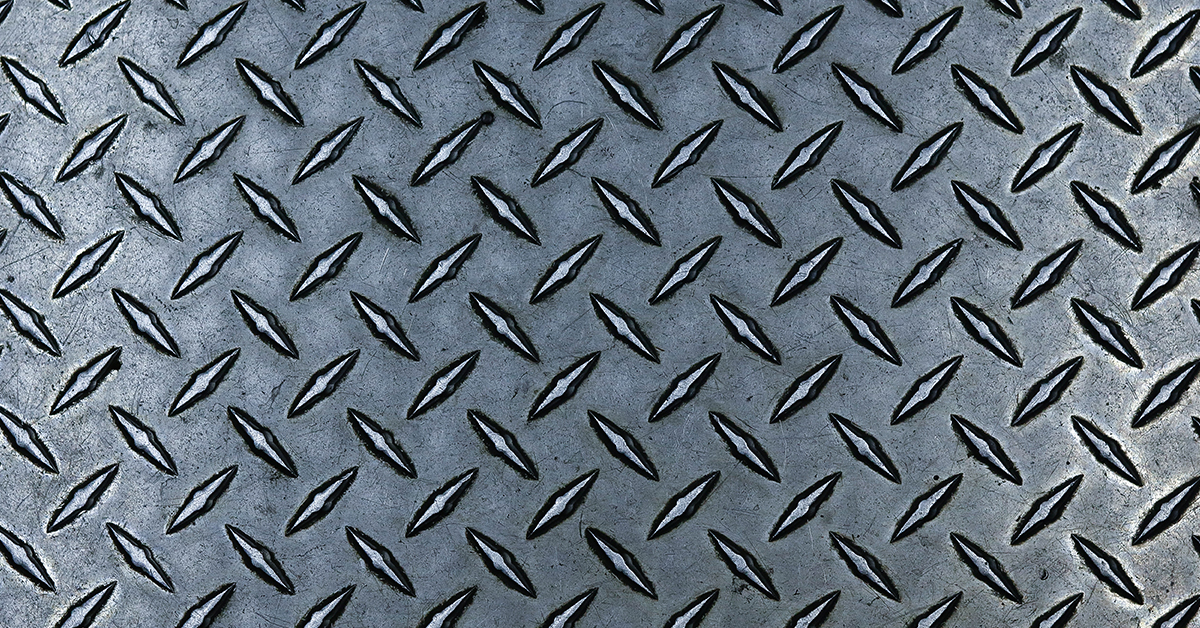
via Unsplash[/caption]As a non-destructive method for inspecting the composition of alloys, PMI testing is efficient for testing large batches of material.
PMI testing for metals and alloys
Determining the precise composition and grade of an alloy helps everyone in the supply chain meet requirements. People that come in contact with the materials along the chain include suppliers, distributors, facility workers, manufacturers, and other responsible parties.Other properties that an alloy can be tested for are
- heat resistance
- durability
- corrosion resistance
- plating thickness
- surface contamination
- sensitization
- grain flow
- weld qualification
Depending on what the metal is going to be used for, other non-destructive and destructive tests can be performed.
Alloy chemical compositions
It’s important to note that each alloy has its own recipe and there are literally hundreds documented in every alloy group.The purpose of alloy groups is to categorize different compositions of metals. For instance, an alloy of nickel with one-third copper is known to resist corrosion from seawater, some acids, and substances involved in petrochemical processing.Here are some more examples of alloy groups:
- Heat-resistant alloys all contain nickel and chromium in order to withstand high operating temperatures.
- Corrosion-resistant alloys — like the one I mentioned above — are intended for use in industrial chemicals, corrosive waters, pollution control, food and beverage processing, and more corrosive environments.
- Special alloys vary in composition and properties. They’re grouped together because their utility depends on mechanical properties (thermal, magnetic, electric) and not necessarily corrosion-resistance or strength.
The Unified Numbering System (UNS) for metals and alloys is the process for designating compositions to groups.
Why is positive material identification important?
Just like we saw with SpaceX’s supplier, there are major ramifications for failing to properly test alloys and metals.
"In the end, it's about quality over profitability." — Chris Carolan
Not only did PMI Industries go out of business, but the quality assurance engineer who falsified 38 inspection reports is under major fire from legal prosecutors. Fortunately for everyone involved, the slip-up has not proven fatal yet.Even so, you can see how easily a person can be harmed from materials failing to undergo accurate PMI testing.
Texas City Refinery explosion
You might remember the explosion that occurred at BP’s Texas City refinery in 2005.Due to numerous organizational and technical failings at the refinery and within BP, 15 people were killed by a hydrocarbon vapor cloud being ignited and exploding. 180 others were injured in the accident.Only a handful of months later, a hydrogen gas heat exchanger pipe overheated and ruptured on the same refinery. The release of hydrogen erupted into a massive fireball. Luckily, only one individual received minor injuries from the eruption.After an investigation of the fireball incident, the Chemical Safety Board uncovered that a contractor had swapped a low-alloy steel elbow with a carbon steel pipe elbow during maintenance.
Proper PMI testing prevents fatalities
If just one defective metal part can cause an enormous fireball, think of the damage faulty metals can do on a larger scale.[caption id="attachment_13283" align="aligncenter" width="1200"]
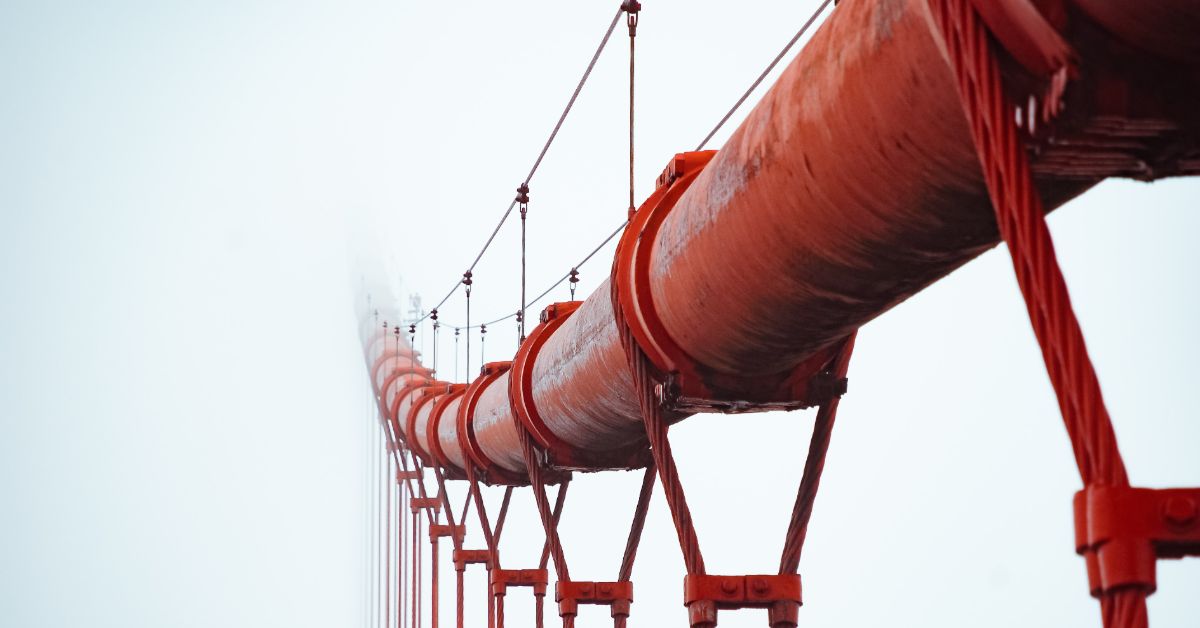
via Unsplash[/caption]Anything made of metal can be subject to improper testing:
- Bridges
- Buildings
- Airplanes
- Vehicles
- Medical devices
- Food processing plants
And, of course, rocket ships.Positive material identification can be the difference between successful production and human fatalities.
When should positive material identification be performed?
Ideally, positive material identification is administered every time a metal changes hands throughout the supply chain.
The metal supply chain
Supply chains for all sorts of materials have become wildly complex. That’s why consumers have taken more interest in where their products or food originate from.Metals are no different. Therefore, it’s crucial to perform PMI testing at every point on the supply chain.
"Globalization has led to a very complex, diverse, and less confident supply chain." — Chris Carolan
Points of the metal supply chain include
- scrap to foundry,
- foundry to parts manufacturer,
- parts to refinery,
- and refinery maintenance and inspection.
PMI testing at each of these checkpoints should be done with the utmost care and attention to detail.
100% PMI is the standard
It used to be that only 10-20 percent of batches needed to be PMI tested. Now, understandably, 100 percent of batches of metals need to be tested before they move on to the next stop on the supply chain.The SpaceX incident demonstrates how crucial it is to test all metal materials before the next step in production. Because the quality assurance engineer falsified many of those tests, billion-dollar projects and unrepeatable work have been compromised.
How do you perform a PMI test?
With any quality assurance testing, costs depend on the industry, urgency, and the critical nature of the application.Whether you choose to hire a consultant, rent PMI testing equipment, or buy the equipment will also vary the prices.
Hiring a positive material identification contractor
If your company doesn’t have the know-how to carry out a positive material identification, hiring a PMI expert is a good idea. Normally, teams of contractors are available for around $300/hour plus the cost of transporting them to the site.Many refineries bring in teams to work 12-hour shifts in order to get maintenance done as quickly as possible.
Renting vs. purchasing PMI equipment
Renting PMI equipment usually runs $2500-$7000 per month depending on the type of tools you choose. Some suppliers, however, offer weekly or even daily rentals.To purchase PMI equipment be prepared to offer up $20k-$40k for handheld tools and up to $60k for the mobile OES. Those prices don’t include the costs of ownership and maintenance.While these prices may sound excessive, they’re nothing compared to the costs or soiled reputation your organization would incur from an accident (think PMI Industries).
How has PMI testing evolved?
It’s clear that globalization has created a more complex and diverse supply chain than ever before. Positive material identification has had to adjust to the vastness of the metal supply chain.[caption id="attachment_13285" align="aligncenter" width="1200"]
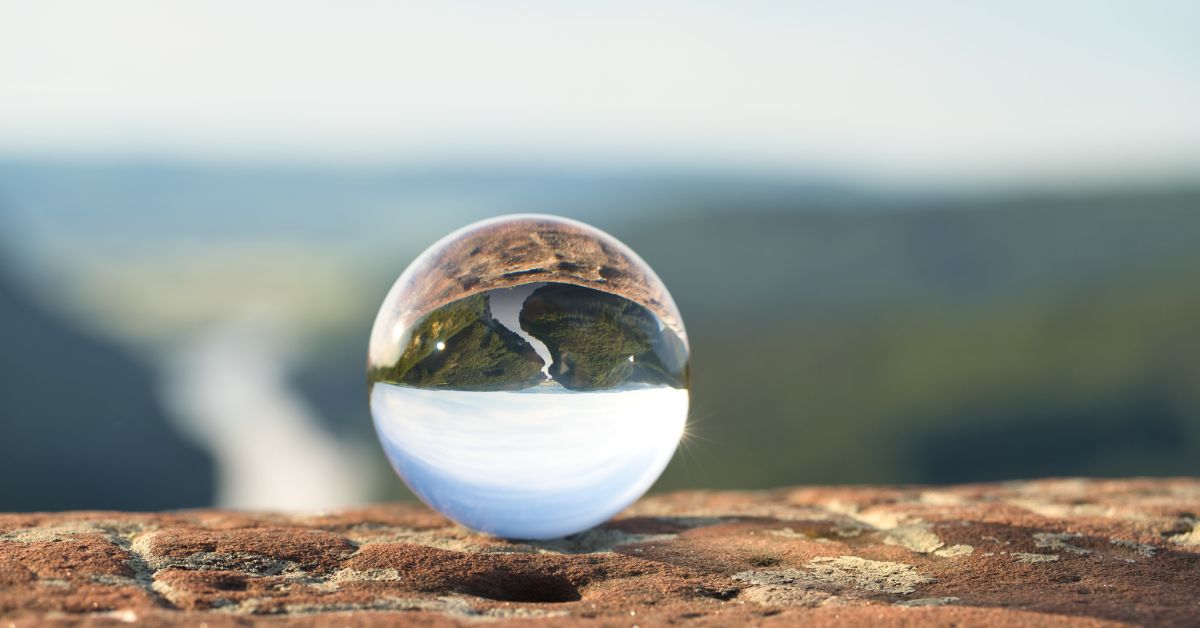
via Unsplash[/caption]Like I mentioned earlier, the percentage of material batches that suppliers are required to test has grown from 10-20 to now 100 percent.Additional recent developments in PMI testing includes
- a better understanding of liability and risk in the metals industry
- quality being prioritized over profitability throughout the metal supply chain
- an improved analyzer performance thanks to lightweight tools, lower detection limits, and easy-to-use software
Not all developments are positive, though. Because the software we have to help us analyze data is so simple to use, valuable training has been pushed to the side.As an industry, we should keep in mind that without a deep understanding of the data we collect, accidents are more probable. Properly training new professionals is crucial to passing on the knowledge and skills we’ve obtained.
Positive material identification verifies the structure of our world
As our world continues to develop with the help of metals, it’s up to quality assurance professionals to carry out accurate positive material identification.
"PMI verifies the structure of the world around us." — Chris Carolan
Remember the lessons we’ve learned from companies like PMI Industries and BP. Preventing accidents and fatalities due to defective alloys starts with honest PMI testing.It affects everything and everyone around us.For more expert insights on PMI testing, subscribe to The Manufacturing Show on Apple Podcasts, Spotify, or wherever you listen to podcasts.